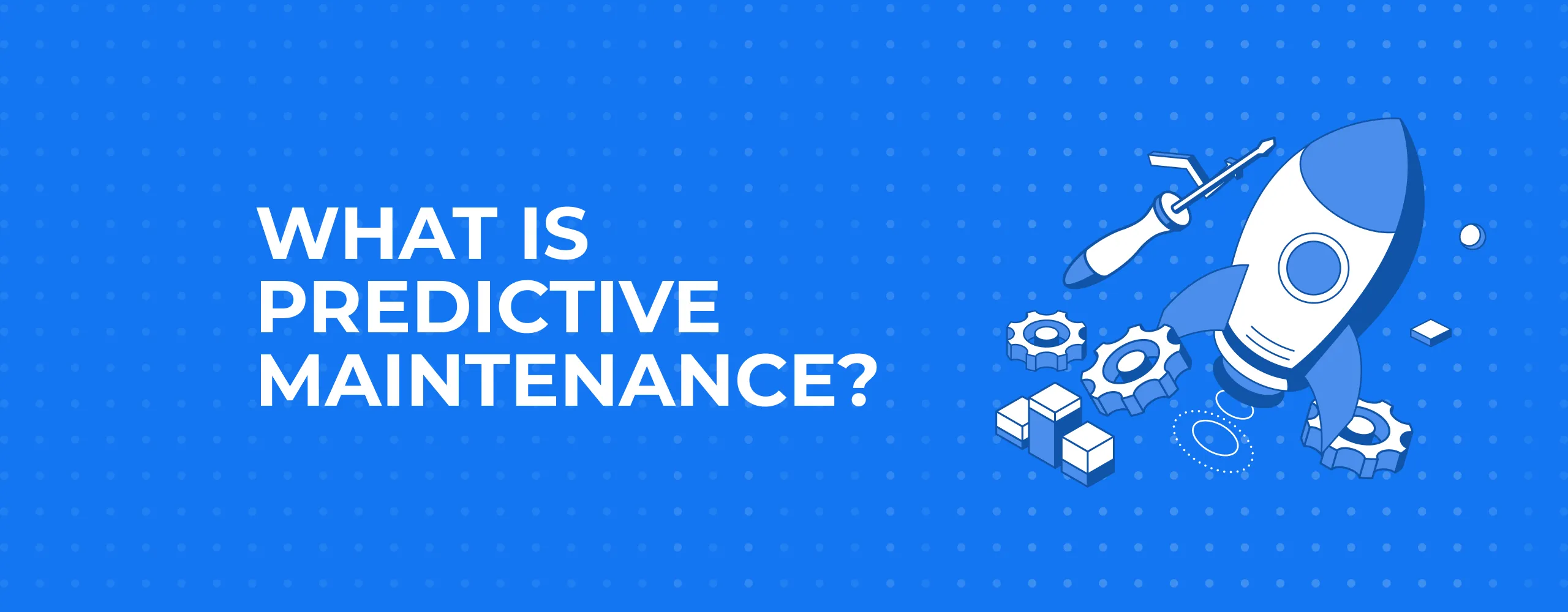
What is predictive maintenance?
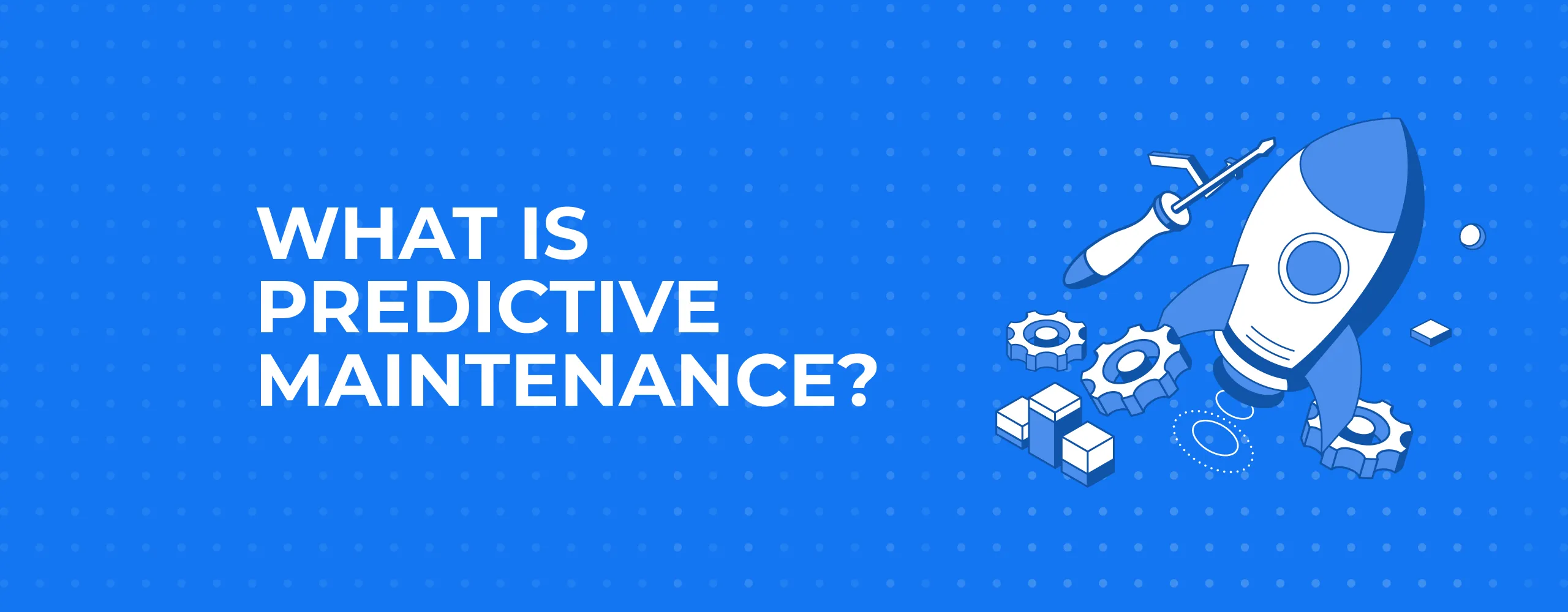
They say, one can predict everything except the future? - oh, you are so off mark!
Predictive maintenance is one of the most seizable applications of Industry 4.0. It can be used to obtain condition data from machines and thus proactively maintain plants. This real-time processing of the underlying data makes forecasts possible, which form the basis for the maintenance as needed and consequently the reduction of downtime. In addition to the interpretation of sensor data, this requires a combination of real-time analysis technology and in-memory database to achieve a higher access speed to the data compared to hard disk drives. If everything works out, it will be possible on the production side to assign a technician to fix a problem even before it arises. After all, economic goals can only be achieved if systems, machines and processes are functioning properly.
However, Predictive maintenance is applicable not only for the world of complicated equipment but also useful in our casual life. If you are looking for handier examples from an everyday world, here is the one. Magora has recently developed an app for avid parents, Misty the Smart Cloud. Misty is a multifunctional super cute and super smart IoT product. A parent can monitor your baby’s nursery temperature; use the personal assistant to record important data such as feeds, health events and diaper changes. Another one is Rotimatic (cuuuuuuute). Rotimatic robot bakes in semi-automatic mode a special kind of bread, Roti, which is very popular with a big part of the multicultural US population. Magora’s challenge was to provide all Rotimatic devices with Artificial Intelligence, let them upgrade themselves and offer remote troubleshooting once connected to WiFi. Development team built a robust server side with a user-friendly control panel, which provides a wide range of distant management capabilities including sensor diagnostics, time/temperature monitoring and recipes update.
How it works
Predictive maintenance categorizes the condition of equipment, which is then being checked either periodically (offline) or continuously (online). Ideally, this makes it possible to schedule upcoming maintenance not only for maximum cost efficiency, but also for maximum performance efficiency, i.e. before the machine is threatened with a loss of performance. To keep interruptions to regular system operation to a minimum, the majority of predictive inspections can be completed in parallel with the operation of the plant. A great illustration of this principle is another Magora case, Maintenance Software. The application encompasses a large amount of features that enable property management companies to arrange a productive dialogue with their residents and organize maintenance workflow.
When used correctly and efficiently, predictive maintenance can deliver a wide range of benefits - for both the manufacturer and the user. Here is an outline of the most important benefits:
Improved cost-effectiveness: On the one hand, predictive maintenance can help to reduce machine and plant downtimes and cut costs for unplanned outages. On the other hand, regular maintenance of machines and systems can also increase their service life.
Optimal maintenance time: With predictive maintenance, the best possible time for maintenance can be determined by permanently evaluating the data recorded. In addition, this allows maintenance to be optimally integrated into the production process.
Improving machine performance: By permanently analyzing the collected data, it is possible to improve the performance of the machine and achieve higher productivity in the long term.
No doubt, predictive maintenance allows the business to offer new services to its customers and has many other benefits. It also helps to increase the quality of your product, improve it based on insights and reduce your support team spendings. By using predictive maintenance you minimize critical and unexpected failures and increase loyalty.
One of the biggest goals of Predictive maintenance is to revolutionize the manufacturing industry by using insights and data to make proactive decisions rather than reactive decisions and optimize key processes. Start to be proactive with Magora Discovery Phase. The team will analyze your business processes and will discover your main challenges whether it is a industrial project, reverse engineering or a just a household appliances.